
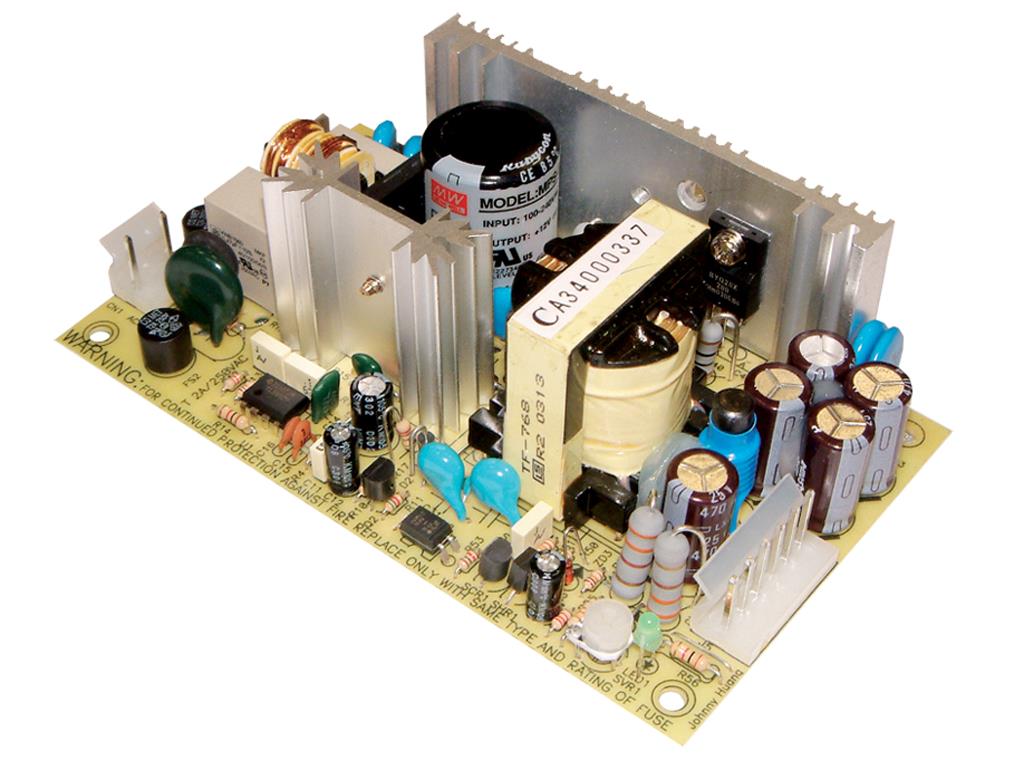
This sounds great for those lower level dependent demand items.
#MPS MEANING UPDATE#
Oh, and what about setting those values for reorder level and order up to level? A good MRP system will have utilities that can look back at historical consumption, recommend values for these settings, and perform the update for you. In practice it is almost “set it and forget it." As long as you have defined appropriate order modifiers (reorder level, outer up to level, order multiple etc.) and you have an accurate lead time and inventory, MRP will do a very good job creating advice in the form of planned orders that ensure material is available when it is needed while keeping inventory to a minimum. No, the algorithm is not simple, quite the opposite, but using MRP to plan an item is simple. This brings us to the first reason for using MRP to plan an item: MRP is simple.

Real world rule number one: keep it simple and justify the addition of complexity Forecasts must always be tweaked for information that is not reflected in historical data. It also will not reflect a sales plan for three major promotions in the coming year when there were only two last year. Historical demand for an item will reflect seasonality, but it cannot reflect the timing of a new product that will be introduced in the coming year that will cannibalize the sales of an existing product. While a statistical forecast can serve as a starting point, human intervention is always ( yes, always) required to fine tune the forecast based on long term and short term shifts in the business plan that are not reflected in the historical data. Forget the idea of relying on statistical techniques to develop the forecast. This sounds good in a text book, but in practice and in my experience, the biggest barrier to adopting MPS is the creation and maintenance of the forecast. Dependent demand items should be MRP planned items as their demand is driving items above them in the BOM and ultimately MPS items.Independent demand items should be MPS items, so we can drive their plan with a sales forecast.So, what does MPS do? The algorithm in MPS is nearly the same as MRP with one important exception: MPS also takes into account a forecast for the item.Ĭonventional thinking suggests two rules of thumb that on the surface sound good but in practice are very difficult to achieve:

These fine-tune the planned order often resulting in larger orders that help address variation in demand and improve order economics, balancing the cost of many small orders versus fewer larger orders. In addition, MRP takes into account item specific order modifiers such as reorder levels, order up to levels, minimum quantities and order multiples. The date the order must be placed based on its lead time so that the supplier or manufacturing has enough time to fulfill it.The date the order is due so that the product arrives in time to meet demand and.The advice that MRP gives us has two dates MRP answers the question: “How much do we need to buy or make based on how much we have, expect to get and expect to consume. Let's start with what I call the “black box” of planning systems: MRP. We will use these definitions as we explore MPS and MRP. Often they are used to make the product, but they are frequently sold as service items. And, they will have demand that is independent, i.e., demand that is driven directly by sales. They will have dependent demand, i.e., demand that is driven by items that appear above them in the BOM. Consider items that are both sold and that appear in a BOM. Hybrid Demand Item: Of course, there are items that do not fit into our neat little definitions. It is important to note that purchased items that are sold are Independent Demand items. These items are often referred to as “top level” items as they frequently have a BOM and are sold. Independent Demand Item: An item whose demand is based on customer demand for that item. These items are often referred to as “lower level” items as they appear in a Bill of Material. Raw materials and subassemblies that are consumed in the manufacturing process are dependent demand items. Defining Demandĭependent Demand Item: An item whose demand is dependent on the demand of items above it in the Bill of Materials (BOM).
#MPS MEANING DRIVER#
When to use MPS versus MRPĭemand is a key driver for any inventory planning system, so let’s first start with a few definitions. In this article, we explore the differences - and similarities - between manufacturing planning systems MPS (Master Production Scheduling) and MRP (Material Requirements Planning), and the business cases that warrant the use of each.
